What is Total Quality Management (TQM)?
Total Quality Management (TQM) is a method for improving a company’s products and services. It involves everyone in the organization in quality improvements. The main goal is to meet or exceed customer expectations, building their satisfaction and loyalty.
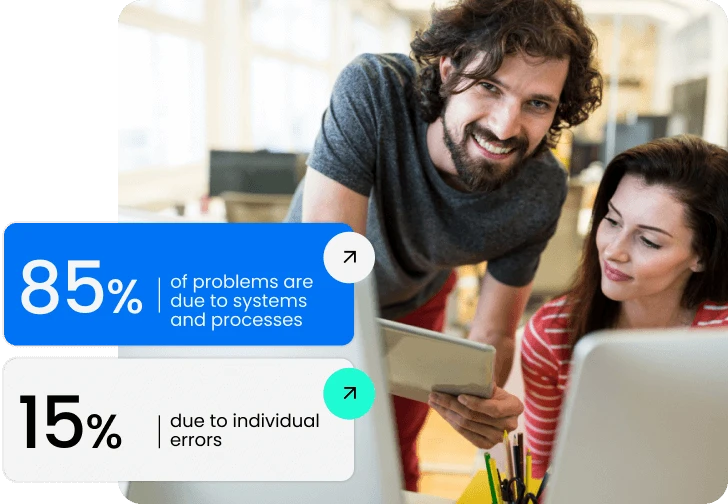
Table of contents
- What is Total Quality Management (TQM)?
- What are the key principles of Total Quality Management?
- Total Quality Management vs Quality Assurance
- Use cases for Total Quality Management
- What are the advantages of Total Quality Management?
- What are the challenges of Total Quality Management?
- How can DAPs help with Total Quality Management?
TQM works by continuously using feedback and data to make better decisions. It focuses on improving every part of the production or service process to reduce waste and increase efficiency. This means everyone, from top leaders to frontline workers, needs to be committed to ongoing training and improvement.
TQM focuses on improving processes instead of blaming individuals for mistakes. This matches Deming’s 85/15 rule, which says 85% of problems are due to systems and processes, and only 15% are due to individual errors.
TQM is reliant on strong leadership, change management, and analysis processes. Kanji states, “To improve performance, people need to know what to do, how to do it, have the right tools to do it, be able to measure performance, and receive feedback on current levels of achievement.”
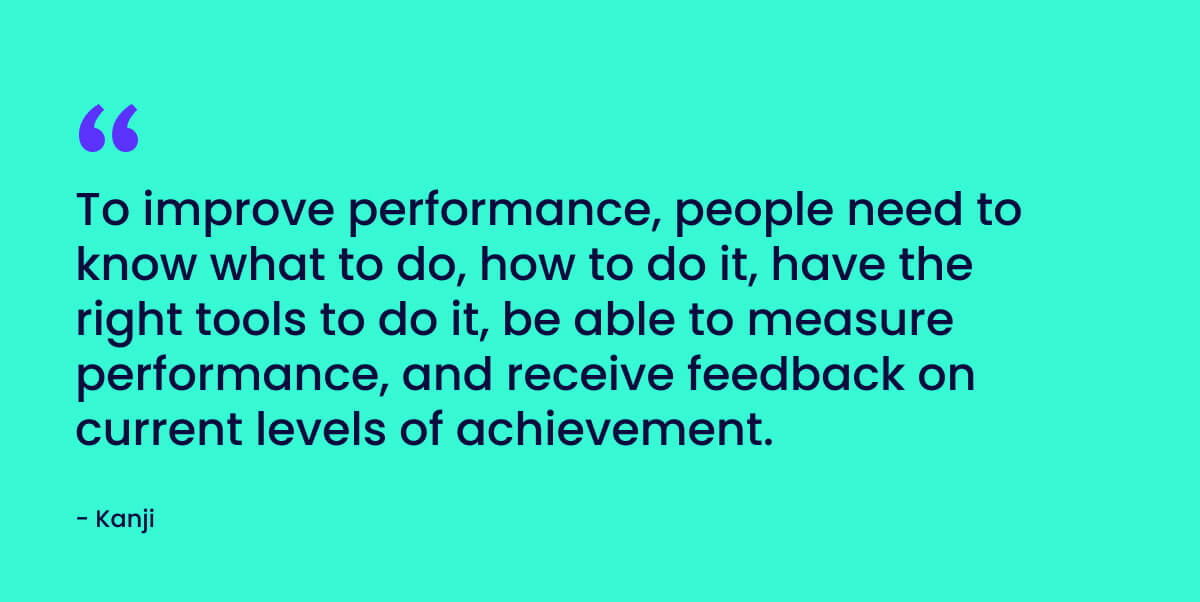
What are the key principles of Total Quality Management?
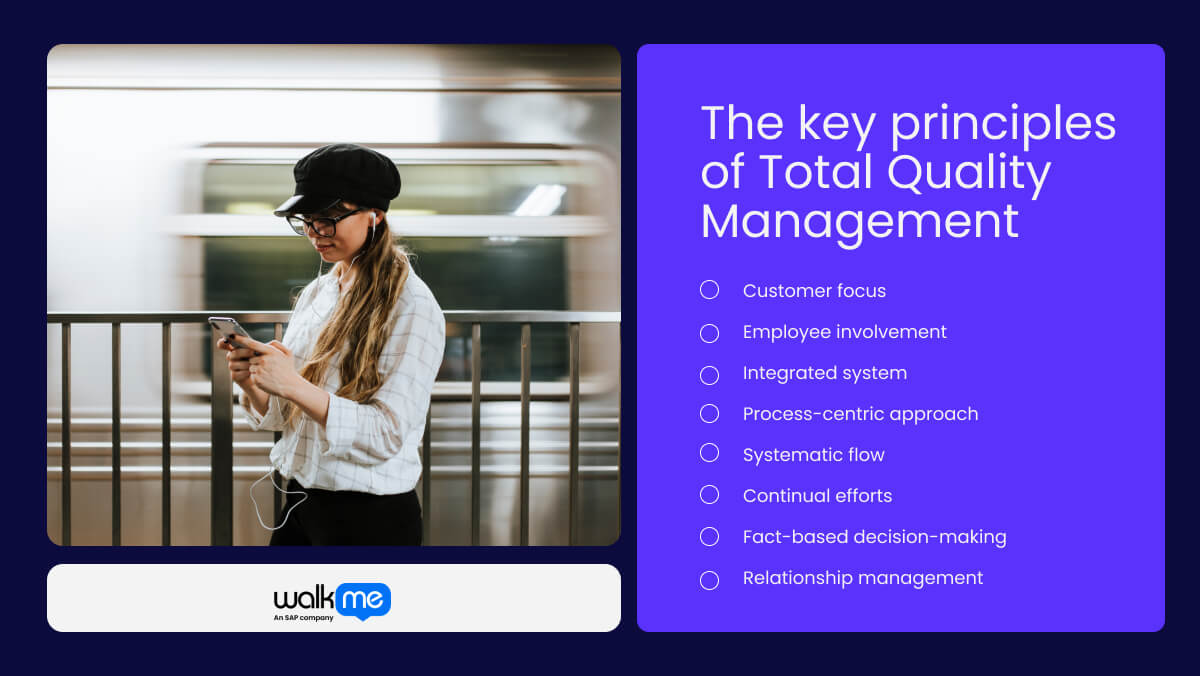
TQM isn’t a one-size-fits-all method. However, eight guiding principles can be used for success.
When applied to TQM, these principles can guide the organization toward continual improvement.
Let’s take a closer look:
Customer focus
The primary aim of TQM is to meet and exceed customer expectations. Organizations prioritize understanding customer needs and preferences. They aim to deliver high-quality products and services. These are designed to enhance customer satisfaction and build long-term loyalty.
Employee involvement
TQM emphasizes the active participation of all employees in the quality improvement process. Workers contribute ideas, solve problems, and take ownership of quality initiatives. Engaging everyone fosters a culture of continuous improvement and shared responsibility.
Integrated system
In TQM, an integrated system means aligning all processes and functions toward quality goals. This principle means creating a unified approach. Every department and team must work together to achieve common quality goals. This will ensure consistency and effectiveness throughout the organization.
Process-centric approach
TQM focuses on improving and optimizing every process within the organization. Businesses can cut inefficiencies and waste and enhance quality by analyzing and refining their processes on an ongoing basis.
Systematic flow
A systematic flow means all quality management practices must be well-organized and structured. This principle stresses the need for a clear, logical order of processes. It should allow smooth, efficient operations and ensure quality results.
Continual efforts
Continual efforts are central to TQM, emphasizing the need for ongoing improvement and refinement. Organizations should always seek to improve their processes, products, and services. They must sustain quality improvements over time and adapt to changing needs.
Fact-based decision-making
Decisions in TQM are based on accurate data and thorough analysis rather than intuition or assumptions. Using facts helps organizations make better choices. This leads to higher-quality outcomes and better problem-solving.
Relationship management
Effective relationship management means building strong ties with all stakeholders, including customers, suppliers, and partners. TQM stresses the need for collaboration and communication with these parties. It is key to achieving quality goals and mutual benefits.
Total Quality Management vs Quality Assurance
Total Quality Management (TQM) and Quality Assurance (QA) ensure high-quality standards. However, they differ in scope and approach.
- TQM is a quality improvement approach. It involves all employees in a quest for constant improvement.
- QA focuses on the processes and standards that ensure products and services meet quality criteria.
Let’s examine the concepts in more depth:
Total Quality Management | Quality Assurance | |
Definition | TQM is a comprehensive management approach. It seeks to improve quality across all organizational processes through continuous improvement and the involvement of all employees. | QA is the systematic process of ensuring that products and services meet predefined quality standards and requirements. It focuses on preventing defects through planned and systematic activities. |
Focus | TQM focuses on holistic quality improvement across the entire organization. It integrates quality into every aspect of operations and engages all employees. | QA focuses on the processes and standards to ensure that products or services meet quality requirements. It is more concerned with verifying and validating outputs to prevent defects. |
Techniques | Continuous improvement (Kaizen)Employee involvement Process management Benchmarking Customer feedback systems | Standards compliance (e.g., ISO standards)Quality audits Process control Testing Documentation |
Goals | To achieve long-term success by embedding quality into every process, increasing customer satisfaction, and fostering a culture of continuous improvement. | To ensure that products and services meet established quality standards and requirements, minimize defects, and ensure reliability and consistency. |
Examples of use | TQM is used in organizations like Toyota and Motorola, focusing on integrating quality improvements into all operations. Comprehensive employee involvement and continuous enhancement lead to better products and services. | QA is used in software development (e.g., through rigorous testing and validation procedures) and manufacturing (e.g., adherence to ISO standards and regular quality audits). It focuses on ensuring that each product or service meets specific quality criteria. |
Use cases for Total Quality Management
It is worth looking at some examples of TQM in action to understand better how it works. We have rounded up a few popular examples below.
Please note that while these companies have reaped benefits from TQM, its effectiveness can vary depending on factors like organizational culture, leadership, and adherence to the eight guiding principles.
Starbucks
Starbucks employs total quality management (TQM) as a cornerstone of its strategy to maintain consistent product quality and customer experiences across its global network of stores.
The company is deeply committed to continuous improvement. It dedicates significant resources to rigorous staff training programs and routinely updates its operational procedures based on customer feedback.
Through strict quality control measures, Starbucks ensures that every cup of coffee and each customer interaction aligns with its high standards. This meticulous approach upholds the company’s reputation and guarantees that customers receive a uniform and exceptional experience, no matter where they are in the world.
Amazon
Amazon applies total quality management (TQM) principles to drive its ongoing efforts to enhance efficiency and elevate customer satisfaction.
The company leverages data-driven decision-making to fine-tune its supply chain and optimize delivery systems, reflecting its commitment to continuous improvement. For example, Amazon’s innovative “Fulfillment Center” design is a testament to this approach, aimed at streamlining operations and reducing delivery times.
This focus on refining processes ensures that customers receive their orders both quickly and accurately, reinforcing Amazon’s reputation for reliability and efficiency.
Apple
Apple integrates total quality management (TQM) by focusing on innovation, product quality, and customer experience.
Apple employs rigorous quality control measures across all design, manufacturing, and distribution stages to ensure its high standards are consistently met. In addition, Apple invests in extensive employee training and actively seeks feedback from its staff to drive ongoing improvements.
This dedication to quality extends to every device and customer interaction, reinforcing Apple’s commitment to excellence and continuous enhancement of its products and services.
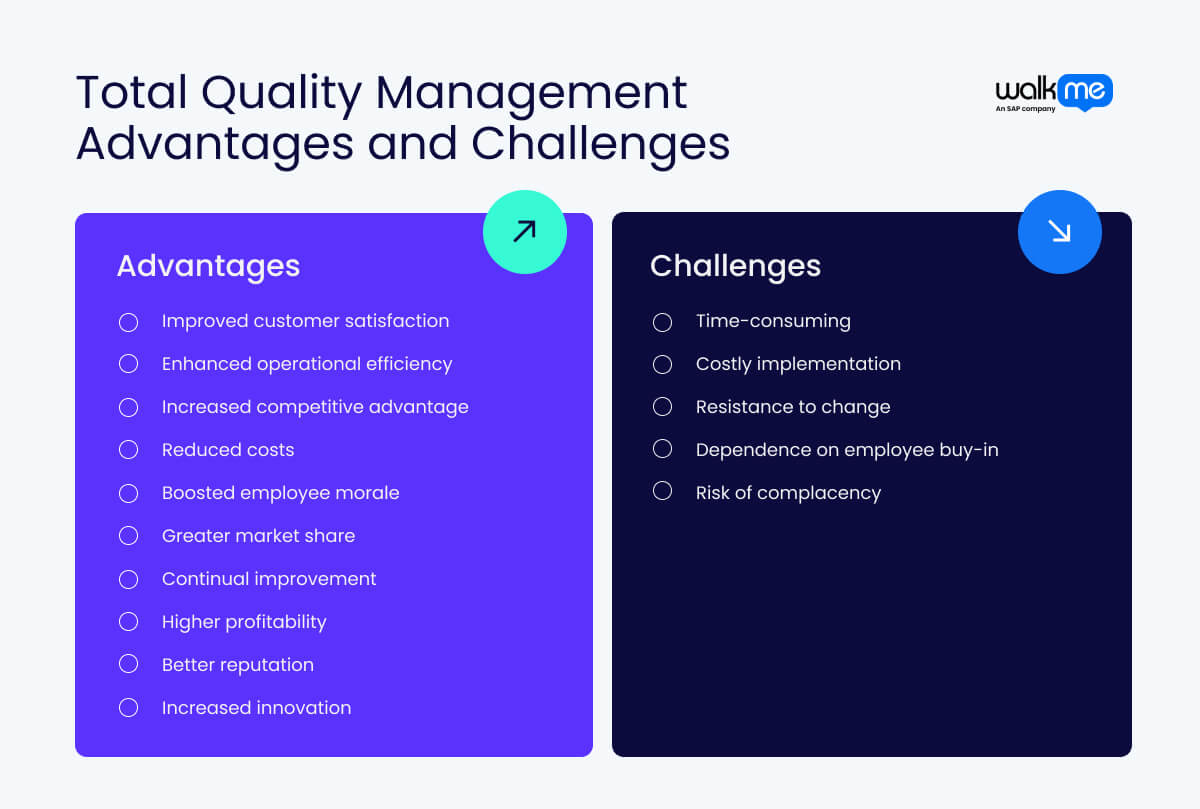
What are the advantages of Total Quality Management?
By this point, it should be clear that Total Quality Management is an extremely valuable tool for any organization.
When implemented effectively and efficiently, TQM can lead to many advantages, such as:
Improved customer satisfaction
TQM focuses on meeting customer needs and exceeding their expectations. Organizations can significantly boost customer satisfaction and loyalty by emphasizing quality and responsiveness, leading to repeat business and positive referrals.
Enhanced operational efficiency
TQM enhances operational efficiency by identifying and eliminating waste. Streamlining workflows, refining processes, and optimizing resource utilization increase productivity and effectiveness, allowing organizations to deliver better results with fewer resources.
Increased competitive advantage
Organizations that effectively implement TQM gain a competitive edge in the market. Delivering consistently high-quality products and services distinguishes them from competitors, helping to attract and retain customers in a crowded marketplace.
Reduced costs
TQM helps organizations reduce costs by systematically identifying and eliminating waste. Improving process efficiency and minimizing defects lead to lower operational expenses and higher profitability.
Boosted employee morale
Involving employees in the quality improvement process fosters a positive work environment. Engaging staff in decision-making and recognizing their contributions enhances morale, job satisfaction, and workplace enthusiasm.
Greater market share
High-quality products and services driven by TQM can enhance a company’s market share. Satisfied customers are more likely to become loyal patrons, which in turn attracts new customers and helps to capture a larger portion of the market.
Continual improvement
TQM instills a culture of ongoing improvement within an organization. Companies stay ahead of industry trends by continually upgrading processes, products, and services and continuously enhancing their operational standards.
Higher profitability
TQM contributes to higher profitability by reducing costs and increasing efficiency. Improved resource management and product quality lead to better financial performance and a stronger bottom line.
Better reputation
Consistently delivering high-quality products and services enhances an organization’s reputation. A strong reputation built on customer satisfaction and trust can increase market opportunities and competitive advantage.
Increased innovation
TQM encourages a focus on constant improvement and problem-solving, which fosters innovation. Organizations are motivated to develop creative solutions and new approaches, driving progress and staying ahead of industry developments.
What are the challenges of Total Quality Management?
While the benefits of TQM are numerous, it is also important to be aware of the potential disadvantages. Let’s look in more detail:
Time-consuming
Implementing TQM requires extensive planning, training, and monitoring. This can be time-consuming and requires a lot of effort from all levels of the organization.
Costly implementation
TQM can have high initial costs. These include training, process improvements, and system upgrades. These costs can be a barrier for some organizations.
Resistance to change
Fear of change may cause resistance to TQM initiatives. Employees and management may be uncomfortable with new processes. This can hinder TQM’s successful adoption.
Dependence on employee buy-in
The success of TQM relies heavily on the commitment and engagement of all employees. Without widespread buy-in, efforts may be ineffective or fail to achieve desired results.
Risk of complacency
Once TQM processes are in place, a risk arises. Organizations might become complacent and stop seeking improvements. This could undermine TQM’s ongoing benefits.
How can DAPs help with Total Quality Management?
Digital adoption platforms (DAPs) support Total Quality Management (TQM) by enhancing how organizations implement and maintain quality practices.
DAPs help ensure quality standards in all operations by providing real-time guidance, enabling efficient training, and promoting consistent process adherence.
Through these capabilities, DAPs contribute to TQM initiatives’ seamless integration and advancement.
Let’s take a closer look:
Facilitating training and onboarding
DAPs offer guided, interactive training for employees. They help workers adapt quickly to new systems and processes. This ensures all team members know quality management practices. They must also understand how to contribute to continuous improvement.
Enhancing process consistency
DAPs offer real-time guidance and support within digital tools and systems. They provide step-by-step instructions and best practices and help ensure processes are consistently followed across the organization. This reduces errors and variability in product and service delivery.
Collecting and analyzing data
DAPs can track user interactions and performance metrics. They provide data on process execution and areas for improvement. This data-driven method supports TQM.
Improving communication and feedback
DAPs often have features for real-time feedback and communication. They let employees report issues and suggest improvements directly through the platform, fostering a culture of improvement and ensuring feedback is used in quality management.
Streamlining change management
Implementing new TQM practices often involves challenges related to change management. DAPs help by guiding employees through new processes. They reduce resistance to change and ensure smooth transitions, helping maintain the momentum of TQM initiatives and enhancing overall adoption and compliance.
Supporting compliance and standardization
DAPs ensure compliance with quality standards and best practices. They do this by providing checks and reminders within digital workflows. It helps ensure consistent quality management. It also supports compliance with industry standards and regulations.
Frequently asked questions
In a Total Quality Management system, every employee has a role to play regardless of their position in the organization. This approach recognizes that quality isn’t just the responsibility of one department or a group of specialists but is everyone’s job. Employees are encouraged to take an active role in quality improvement by identifying problems and inefficiencies in their work processes and proposing solutions. They may be involved in quality circles or improvement teams, where they can share ideas and collaborate on solutions. This involvement helps improve quality and fosters a sense of ownership and engagement among employees.
TQM’s ultimate goal is to exceed customer expectations and achieve customer satisfaction. This is accomplished by continually improving the quality of products and services based on customer feedback and preferences. In a TQM system, customer feedback is not just collected but is meticulously analyzed and used as a basis for improvements. If a product fails to meet customer expectations, the TQM approach would be to investigate the process that produced the product, identify the root cause of the problem, and make necessary improvements to prevent the same issue from happening in the future.
Yes, TQM principles can be applied to all kinds of organizations, whether in the manufacturing, service, non-profit, or government sectors. The key is to understand that TQM is not a one-size-fits-all solution but needs to be tailored to fit each organization’s unique needs and characteristics. Implementing TQM requires a commitment from top management and a willingness to foster a culture of continuous improvement throughout the organization. While the specific processes and tools used may vary, the underlying principles of customer focus, employee involvement, and continuous improvement remain the same.
By clicking the button, you agree to the Terms and Conditions.
Click Here to Read WalkMe’s Privacy Policy