What are Quality Management Systems?
Quality Management Systems (QMS) are structured frameworks and processes implemented by organizations to ensure that they consistently meet or exceed the customer experience in terms of product or service quality.
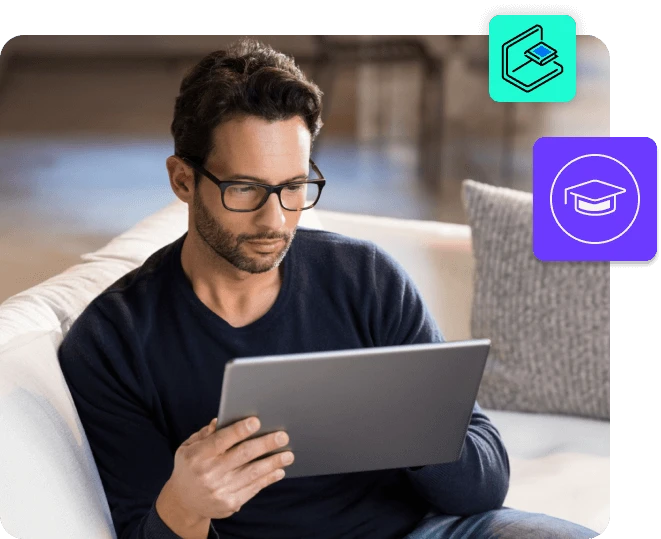
Table of contents
- What are Quality Management Systems?
- Types of Quality Management System
- Quality Management Systems in the workplace
- QMS in practice
- What are the benefits of Quality Management Systems?
- Quality Management Systems vs Quality Assurance vs Quality Control Plan
- Big businesses and QMS
- How to choose a Quality Management System
- How is a Quality Management System rolled out?
The primary goal of a Quality Management System is to establish a systematic and organized approach to managing and improving quality across all aspects of an organization.
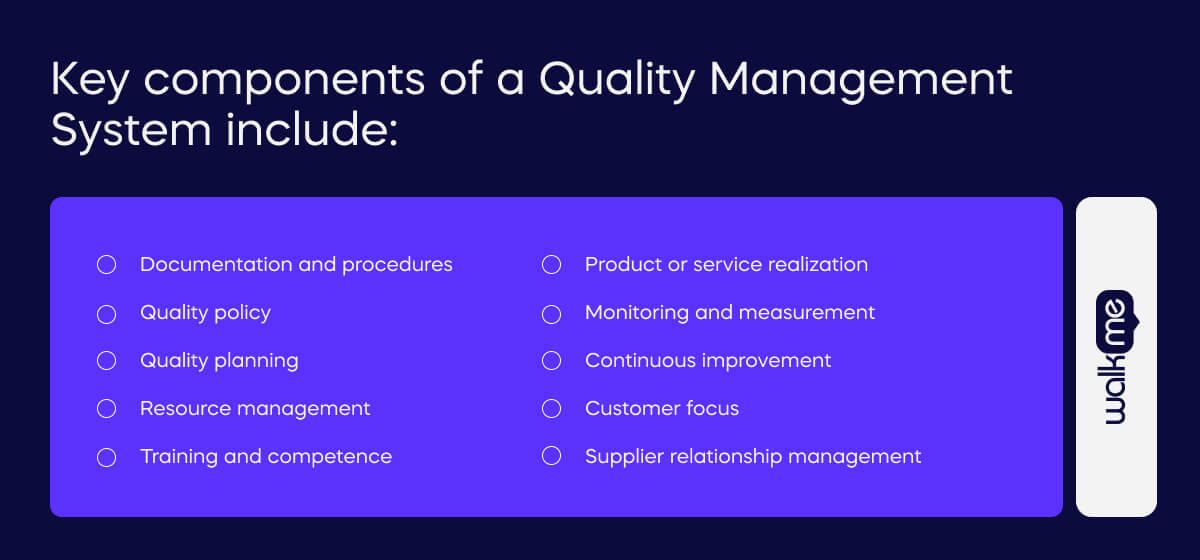
Key components of a Quality Management System include:
Documentation and procedures
Documented policies, procedures, and work instructions guide employees in carrying out their tasks in a standardized and quality-focused manner.
Quality policy
A statement by top management expressing the organization’s commitment to quality and outlining the overall quality objectives.
Quality planning
Identifying quality objectives and the processes needed to deliver a product or service that meets customer requirements.
Resource management
Ensuring that the organization has the necessary resources (human, technological, financial) to achieve its quality objectives.
Training and competence
Providing employees with the necessary skills and knowledge to perform their tasks effectively and in accordance with quality standards.
According to Statista, the average spend per employee on learning and development increased in 2021 to almost $1300 per worker, indicating that companies recognize the benefit of ongoing training.
Product or service realization
Managing the processes involved in creating a product or delivering a service to ensure consistency and quality.
Monitoring and measurement
Implementing systems to monitor and measure processes, products, and services to ensure they meet predefined quality standards.
Continuous improvement
Establishing mechanisms for ongoing evaluation and enhancing processes to achieve better performance and customer satisfaction.
Customer focus
Placing a strong emphasis on understanding and meeting the voice of the customer and their expectations.
Supplier relationship management
Establishing and maintaining strong relationships with suppliers to ensure the quality of inputs into the organization’s processes.
Types of Quality Management System
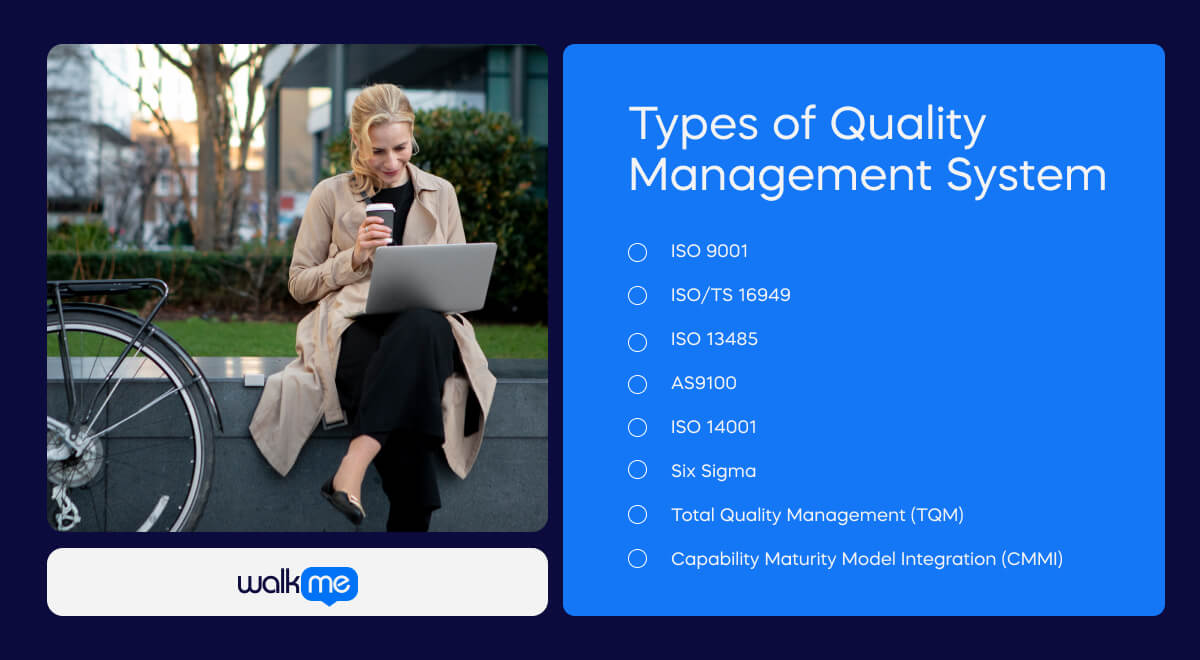
There are several types of Quality Management Systems (QMS), and organizations can choose the one that best fits their industry, specific needs, and objectives.
One of the most widely recognized QMS standards is the ISO 9001 standard. Organizations can seek certification to demonstrate compliance with ISO 9001, a globally recognized benchmark for quality management.
Some of the notable QMS frameworks include:
ISO 9001
The International Organization for Standardization (ISO) is a globally recognized standard that sets out the criteria for a quality management system. It applies to any organization, regardless of its size or industry. ISO emphasizes customer satisfaction, continuous improvement, and a process-oriented approach.
ISO/TS 16949
This standard, now known as IATF16949, is designed for the automotive industry. It aligns with ISO 9001 but includes additional automotive-specific requirements to ensure quality and safety in producing automotive products.
ISO 13485
This standard is intended for organizations involved in designing, developing, producing, installing, and servicing medical devices. ISO 13845 specifies requirements for a quality management system where an organization must consistently demonstrate its ability to provide medical devices and related services.
AS9100
This standard is specific to the aerospace industry and incorporates the ISO 9001 requirements and additional criteria relevant to aerospace manufacturing and maintenance.
ISO 14001
While not exclusively a quality management standard, ISO 14001 focuses on environmental management. Organizations implementing ISO 14001 aim to minimize their environmental impact. It can be integrated with ISO 9001 for a combined Quality and Environmental Management System (QEMS).
Six Sigma
While not a specific standard, Six Sigma is a methodology that focuses on process improvement and reducing variation. It aims to achieve near-perfect results by identifying and removing the causes of defects and errors.
Total Quality Management (TQM)
TQM is a holistic approach to quality that involves everyone in the organization in a continuous effort to improve quality and customer satisfaction. It’s a philosophy that extends beyond specific standards and emphasizes a culture of quality.
Capability Maturity Model Integration (CMMI)
Developed by the Software Engineering Institute (SEI), CMMI provides a framework for process improvement across various industries, including software development and systems engineering.
Quality Management Systems in the workplace
Quality Management Systems (QMS) can be tailored to various sectors and industries to ensure that they meet the specific needs and requirements of each.
Here are examples of how QMS may be implemented in different sectors:
Finance
ISO 9001 certification: Financial institutions can adopt ISO 9001 to ensure the quality of their processes, from customer service to transaction handling.
Risk management frameworks: Implementing robust risk management practices to ensure the security and integrity of financial transactions.
Marketing
Customer feedback and satisfaction surveys: Regularly collect and analyze customer feedback to identify areas for improvement.
Campaign performance metrics: Monitoring and evaluating the success of marketing campaigns using key performance indicators.
Banking
ISO 9001 certification: Ensuring that banking processes meet international quality and customer satisfaction standards.
Security protocols: Implementing and continuously improving security measures to protect customer data and financial transactions.
Retail
Inventory management systems: Implement systems to track inventory levels and ensure product availability.
Customer service protocols: Establishing standardized procedures for handling customer inquiries, returns, and complaints.
Insurance
ISO 9001 certification: Ensuring that insurance processes meet quality standards and are customer-focused.
Claims processing efficiency: Establishing streamlined processes for handling and processing insurance claims.
Healthcare
ISO 9001 or ISO 13485 certification: For healthcare providers, ensuring quality in patient care, medical services, and equipment.
Electronic Health Record (EHR) systems: Implementing and maintaining secure and accurate electronic health records.
Manufacturing
Six Sigma methodology: Employing Six Sigma to reduce defects and improve manufacturing processes.
Total Quality Management (TQM): Focusing on a holistic approach to quality, involving all employees in continuous improvement efforts.
Information Technology (IT)
Capability Maturity Model Integration (CMMI): Ensuring the maturity and quality of software development and IT processes.
Service Level Agreements (SLAs): Defining and adhering to SLAs to meet client expectations in IT services.
Education
ISO 9001 certification: Ensuring the quality of educational processes, from curriculum development to student services.
Continuous improvement in teaching methods: Implementing feedback mechanisms and professional development programs for educators.
QMS in practice
Let’s consider an example of a Quality Management System (QMS) for a manufacturing company.
In this case, we’ll imagine a company that produces electronic gadgets and they have implemented a QMS based on the ISO 9001 standard:
Quality policy
The company establishes a quality policy that reflects its commitment to producing high-quality electronic gadgets and meeting customer expectations. The policy is communicated to all employees.
ISO 9001 certification
A company pursues ISO 9001 certification to ensure its quality management system meets international standards. This involves a thorough review and documentation of all processes.
Documented procedures
Standard Operating Procedures (SOPs) are developed and documented for key processes like design, manufacturing, testing, and shipping. These procedures provide a step-by-step guide for employees to follow.
Risk management
A risk management process is implemented to identify potential risks in the manufacturing process, supply chain, and product design. Mitigation plans are developed to address and minimize these risks.
Training and competence
Employees undergo training programs to ensure they have the necessary skills and knowledge to perform their tasks effectively. Competence assessments are conducted periodically.
Product development
A structured product development process is established, including design reviews, prototype testing, and validation procedures. This ensures that new gadgets meet both internal and customer specifications.
Supplier quality management
The company maintains strong relationships with suppliers and establishes criteria for selecting and evaluating suppliers. Regular audits and assessments are conducted to ensure that incoming materials meet quality standards.
Testing and inspection
Comprehensive testing protocols are implemented at various stages of the manufacturing process. This includes in-process inspections, final product testing, and quality control checks to identify and address defects.
Customer feedback
Mechanisms are in place to collect and analyze customer feedback. Customer complaints are investigated, and corrective actions are taken to prevent recurrence.
Continuous improvement
The company fosters a culture of continuous improvement. Regular management reviews are conducted to assess the performance of the QMS, identify areas for improvement, and implement corrective and preventive actions.
Key performance indicators (KPIs)
Key performance indicators, such as defect rates, on-time delivery, and customer satisfaction scores, are established and monitored regularly to gauge the effectiveness of the QMS.
What are the benefits of Quality Management Systems?
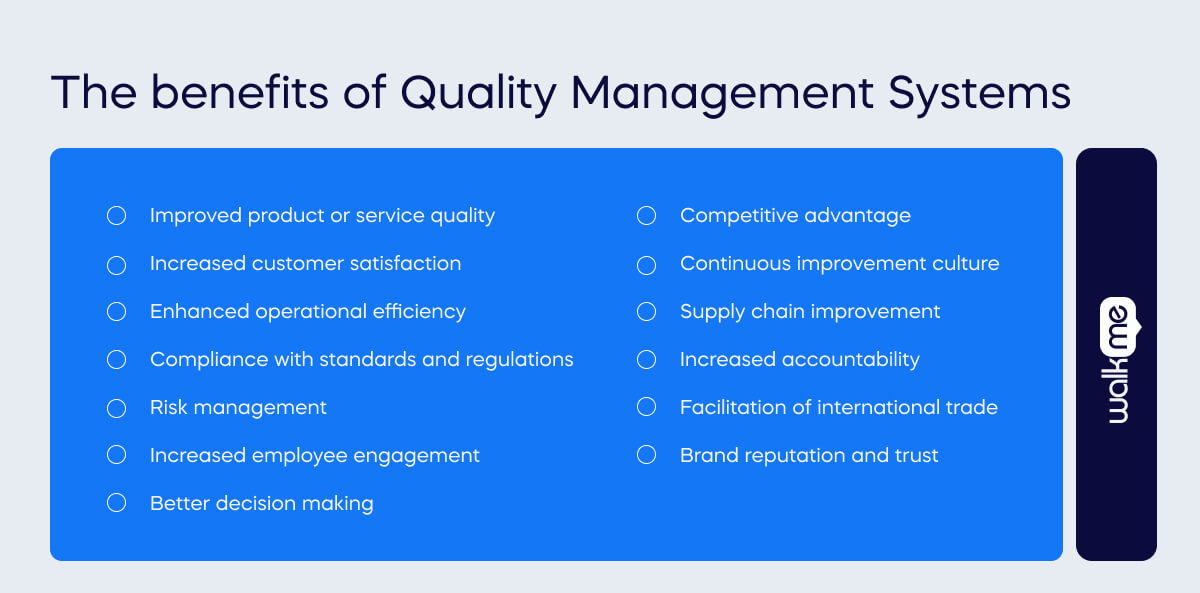
Implementing a Quality Management System (QMS) offers a range of benefits to organizations across different industries. Here are some of the key advantages:
Improved product or service quality
A QMS helps organizations establish and maintain consistently high standards, improving product or service quality. This, in turn, contributes to customer delight and loyalty.
Increased customer satisfaction
By focusing on meeting or exceeding customer expectations, QMS helps enhance customer satisfaction. It involves listening to customer feedback, addressing concerns, and continually improving processes to meet customer needs.
Enhanced operational efficiency
QMS promotes streamlined and standardized processes, reducing inefficiencies and errors. This leads to improved operational efficiency, decreased waste, and cost savings.
Compliance with standards and regulations
Implementing a QMS, especially one certified to international standards such as ISO 9001, ensures that an organization complies with industry-specific regulations and meets recognized quality benchmarks.
Risk management
QMS includes mechanisms for identifying, assessing, and managing risks. This proactive approach to risk management helps organizations anticipate challenges, prevent issues, and respond effectively to unexpected events.
Taking such an approach would assist many businesses, according to statistics from McKinsey’s ‘The State of Organizations 2023.’ The report highlights that only half of surveyed business leaders believe their organizations are well prepared to anticipate and react to external shocks. This suggests a need for organizational risk management to be improved.
Increased employee engagement
Engaged employees are more likely to contribute positively to the organization. QMS involves training, communication, and empowerment, fostering employees’ sense of responsibility and pride.
Better decision making
QMS provides reliable data through monitoring and measurement processes. This data supports informed decision-making at all levels of the organization, contributing to strategic planning and goal achievement.
Competitive advantage
Organizations with effective QMS often gain a competitive advantage. Certification to recognized standards, such as ISO 9001, can be a market differentiator, attracting customers who prioritize quality in products or services.
Continuous improvement culture
QMS promotes a culture of continuous improvement. Regular reviews, feedback mechanisms, and corrective actions contribute to an environment where employees are encouraged to seek better ways of doing things.
Supply chain improvement
Establishing strong relationships with suppliers and implementing supplier quality management processes contribute to a more reliable and efficient supply chain, reducing the risk of disruptions.
The Gartner Supply Chain Top 25 report indicates that superior supply chains are digital-first, customer-driven, and purpose-led.
Increased accountability
Clearly defined roles, responsibilities, and processes within a QMS increase accountability. Employees understand their roles in delivering quality and contributing to a more efficient and responsible organizational structure.
Facilitation of international trade
For organizations involved in international trade, adherence to recognized quality standards facilitates smoother transactions and partnerships. Many global clients and partners prefer to work with certified QMS organizations.
Brand reputation and trust
Consistently delivering high-quality products or services builds trust with customers and stakeholders. A positive reputation for quality contributes to brand strength and longevity.
Quality Management Systems vs Quality Assurance vs Quality Control Plan
Quality Management Systems (QMS), Quality Assurance (QA), and Quality Control (QC) are related concepts, but they represent different aspects of the overall quality management process.
Let’s clarify the distinctions:
Quality Management Systems (QMS) | Quality Assurance (QA) | Quality Control (QC) Plan | |
Definition | A comprehensive framework of policies, processes, and procedures designed to ensure that an organization consistently delivers products or services that meet or exceed customer expectations | Refers to the planned and systematic activities implemented within a QMS to provide confidence that a product or service will fulfill quality requirements | A set of specific activities and techniques used within the QA framework to monitor, inspect, and verify that the product or service meets predefined quality standards |
Focus | Focuses on the entire organization and its commitment to quality. It encompasses strategic planning, process management, documentation, training, and continuous improvement | Process-oriented, aiming to prevent defects by establishing and maintaining processes that ensure quality throughout the entire product lifecycle | Product-oriented involves the inspection and testing of individual products or services at various stages of production to identify and correct defects |
Objective | The primary goal is to establish a systematic and structured approach to quality that permeates all aspects of an organization | The main objective is to assure management and stakeholders that processes are effective and that the organization can deliver a high-quality product or service | The primary objective is to detect and correct defects in the final product, ensuring that it conforms to the specified quality criteria |
Big businesses and QMS
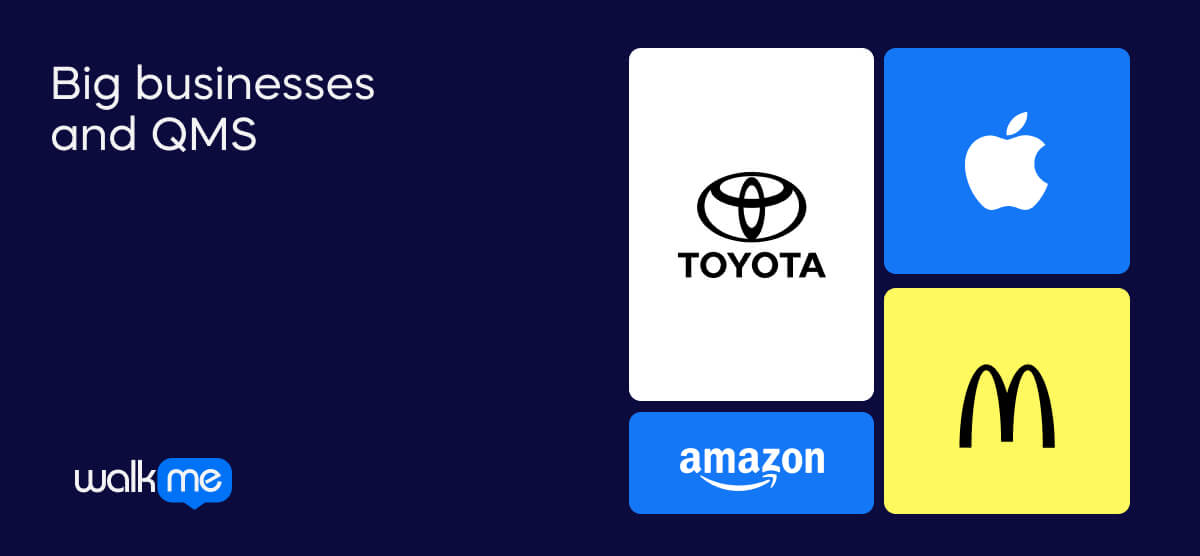
Some companies are known for implementing robust quality practices.
Here are examples of well-known brands and the principles of quality management they are associated with:
Toyota
QMS approach: Toyota is renowned for implementing Lean and the Toyota Production System (TPS). These systems emphasize continuous improvement, waste reduction, and a focus on customer value.
Benefits: Toyota’s commitment to quality has contributed to its reputation for producing reliable and durable vehicles. The principles of Lean and TPS have helped minimize defects, reduce lead times, and optimize production efficiency.
Apple
QMS approach: Apple strongly emphasizes design, innovation, and supply chain management. The company has specific quality standards for product design, manufacturing processes, and component sourcing.
Benefits: Apple’s QMS has contributed to its brand loyalty and market dominance. Products are known for their quality, reliability, and seamless user experience. Rigorous supplier quality management also ensures the consistency of components.
McDonald’s
QMS approach: McDonald’s has implemented a standardized and consistent approach to food preparation, service, and cleanliness across its global chain. This includes detailed operational procedures, training programs, and quality checks.
Benefits: McDonald’s QMS helps ensure that customers receive a consistent experience and quality of food at any of its locations worldwide. This consistency is a key factor in the success and global appeal of the brand.
Amazon
QMS approach: Amazon emphasizes a customer-centric approach to quality, focusing on efficient order fulfillment, reliable delivery, and customer satisfaction. The company employs sophisticated quality control measures in its logistics and fulfillment operations.
Benefits: Amazon’s QMS contributes to its reputation for fast and reliable service. The company’s commitment to quality in logistics and customer service has played a significant role in its growth and dominance in the eCommerce industry.
How to choose a Quality Management System
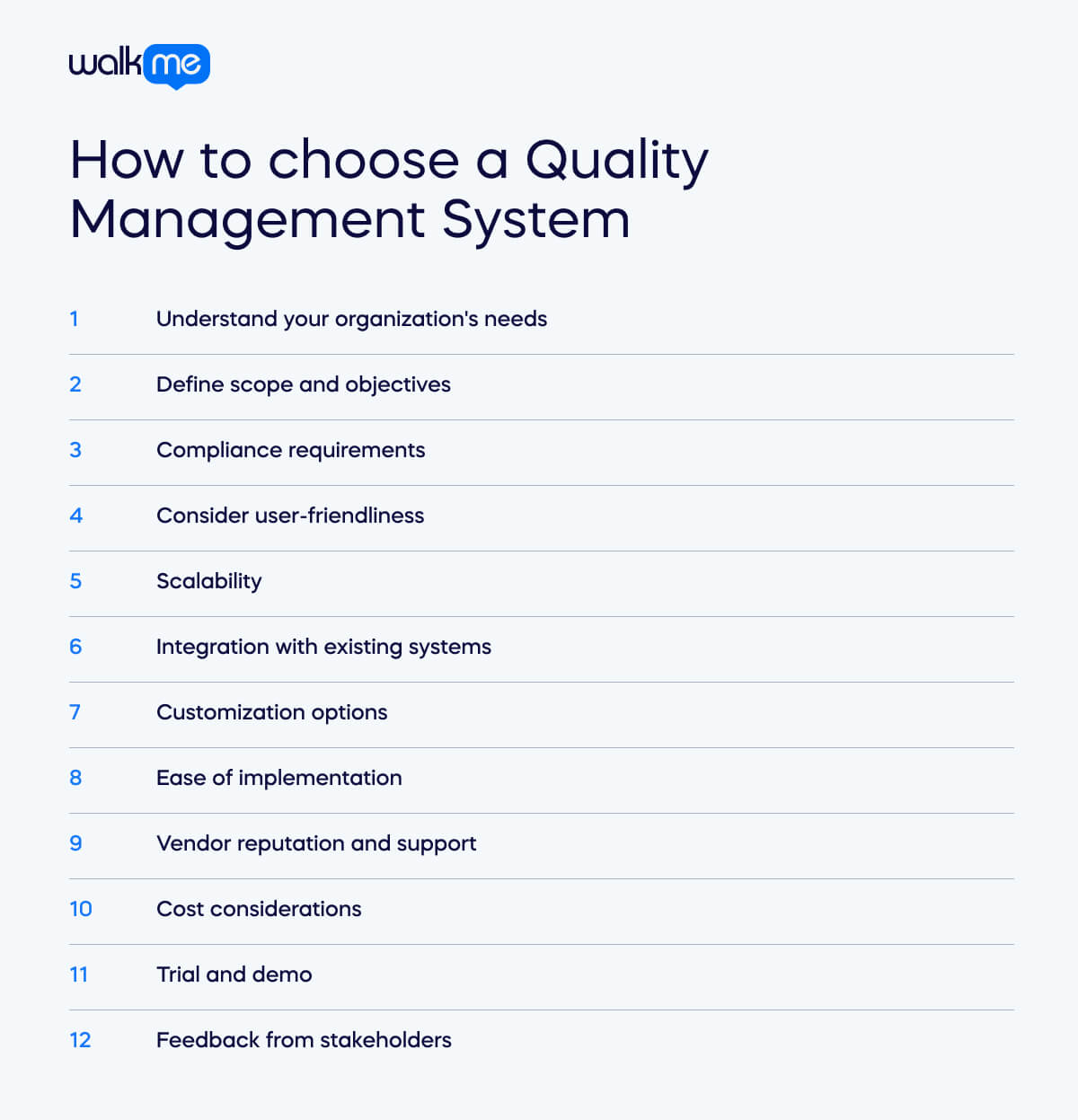
When choosing a QMS, organizations should consider their industry requirements, customer expectations, and the specific aspects of their operations that need improvement. Many organizations also develop customized QMS based on their unique needs and goals.
Choosing the right Quality Management System (QMS) for your organization is a critical decision that can impact your overall quality performance and business success.
Here are steps to guide you in choosing a QMS:
Understand your organization’s needs
Conduct a thorough assessment of your organization’s specific needs, objectives, and challenges. Identify the key processes that require improvement and the goals you want to achieve with the implementation of a QMS.
Define scope and objectives
Clearly define the scope and objectives of your QMS. Determine whether you need a comprehensive QMS that covers the entire organization or if a specific focus (e.g., product development, customer service) is required.
Compliance requirements
Identify the industry-specific regulations, standards, and certifications relevant to your organization. Ensure that the QMS you choose supports compliance with these requirements, whether it’s ISO standards, industry-specific regulations, or customer-specific standards.
Consider user-friendliness
Choose a user-friendly QMS that aligns with your organization’s technical capabilities. The system should be easy to navigate, and its features should be accessible to users with various levels of technical expertise.
Scalability
Consider the scalability of the QMS. Ensure that the system can grow with your organization and accommodate changes in the scale of your operations. This is crucial for long-term sustainability and adaptability.
Integration with existing systems
Evaluate how well the QMS can integrate with your existing software and systems (e.g., ERP, CRM). Integration ensures smooth data flow, reduces redundancy, and facilitates a holistic view of your organization’s processes.
Customization options
Assess the level of customization offered by the QMS. Your organization’s processes and requirements may be unique, and the ability to tailor the QMS to fit your specific needs is essential for its effectiveness.
Ease of implementation
Consider the ease and speed of implementation. A QMS that is straightforward to implement can save time and resources. Additionally, check if the QMS provider offers training and support during implementation.
Vendor reputation and support
Research the reputation of the QMS vendor. Look for customer reviews, testimonials, and case studies. Ensure that the vendor provides adequate support, training, and resources to assist your organization in maximizing the benefits of the QMS.
Cost considerations
Evaluate the total cost of ownership, including initial setup costs, licensing fees, and ongoing maintenance expenses. Consider both short-term and long-term costs to ensure the investment aligns with your budget and expected return on investment.
Trial and demo
Request a trial or demo of the QMS to get hands-on experience with the system. This allows you to assess its functionality, user interface, and overall suitability for your organization before making a final decision.
Feedback from stakeholders
Involve key stakeholders in the decision-making process. Gather input from users, managers, and other relevant parties to ensure that the chosen QMS meets the needs and expectations of everyone involved.
How is a Quality Management System rolled out?
Rolling out a Quality Management System (QMS) is a structured and phased process that involves planning, implementation, and ongoing monitoring. Here are general steps to guide the rollout of a QMS:
Leadership commitment and planning
Leadership commitment: Ensure top management commitment to the implementation of the QMS. This commitment is crucial for securing necessary resources and fostering a quality-oriented culture.
Planning: Develop a detailed project plan outlining the scope, objectives, timeline, and resources required for the QMS implementation.
Assemble a QMS team
Form a dedicated QMS implementation team with representatives from different departments. This team will coordinate the rollout, communicate changes, and ensure compliance.
Training and awareness
Provide training to employees at all levels to create awareness about the QMS, its benefits, and their roles in the implementation. This may include training on QMS principles, processes, and any new tools or technologies.
Document current processes
Document existing processes within the organization. This includes creating process maps, standard operating procedures (SOPs), and work instructions. This step is crucial for understanding the current state of operations.
Risk assessment and gap analysis
Conduct a risk assessment to identify potential risks to quality and compliance. Perform a gap analysis to compare existing processes with the requirements of the QMS standard chosen (e.g., ISO 9001). This helps identify areas that need improvement.
Define QMS processes
Develop and define the QMS processes based on the QMS standard and the organization’s specific needs. This involves creating new processes, updating existing ones, and aligning them with the QMS framework.
Implementation of QMS processes
Begin implementing the defined QMS processes in a phased approach. This may involve changes to procedures and workflows and introducing new tools or software to support QMS activities.
Communication and change management
Communicate the changes and updates to all employees. Implement change management strategies to address any resistance and ensure a smooth transition. Encourage feedback and open communication channels.
Documentation and record-keeping
Ensure proper documentation and recordkeeping for all QMS processes. This includes maintaining records of training, audits, corrective actions, and any other relevant activities. Documentation is essential for demonstrating compliance during audits.
Internal audits
Conduct internal audits to assess the effectiveness and compliance of the QMS processes. Internal audits help identify areas for improvement and ensure ongoing adherence to QMS standards.
Management review
Schedule regular management reviews to evaluate the performance of the QMS. Management reviews involve assessing key performance indicators, reviewing audit results, and making decisions for improvement.
Continuous improvement
Foster a culture of continuous improvement. Encourage employees to suggest improvements, analyze data, and implement corrective and preventive actions to enhance the effectiveness of the QMS.
External certification (if applicable)
If seeking external certification, conduct an external audit with a certification body. Achieving certification demonstrates that the organization’s QMS meets international standards.
Ongoing monitoring and review
Continuously monitor and review the QMS to ensure its ongoing effectiveness. This includes periodic internal audits, management reviews, and addressing any emerging issues or organizational changes.
Documentation of lessons learned
Document lessons learned throughout the QMS rollout. This documentation can inform future improvements, provide insights for other projects, and contribute to the organization’s overall knowledge base.