What Is QMS?
A quality management system or QMS helps companies systematically document business processes and procedures that are essential for the successful delivery of consumer-based products and services. Quality management systems are used to enhance customer satisfaction through the delivery of high-quality products and services.
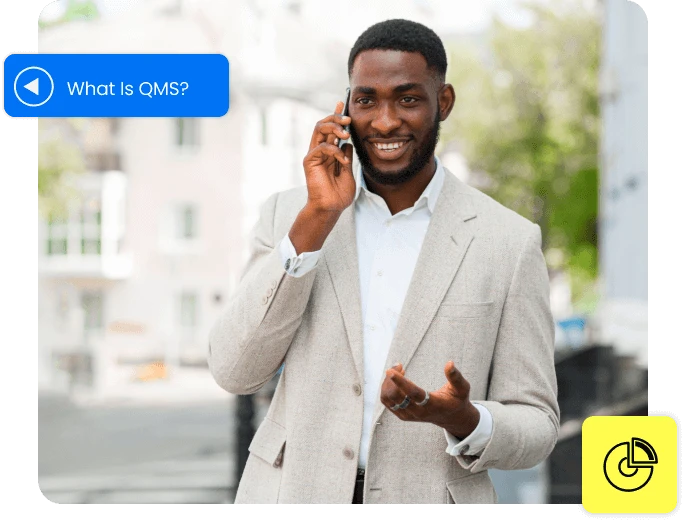
Table of contents
QMS frameworks help to steer businesses towards quality goals through the fulfillment of customer needs. An effective QMS incorporates the business activities associated with the production process and streamlines performance by adopting uniform skills, methods, and resources to strengthen customer satisfaction and retention.
QMS Structure
Implementing a QMS structure aids observance, profitability, and the advancement of a quality-driven culture.
There are 5 core elements of a quality management system:
1. Quality Policy & Objectives – The first step in building a quality management system is to formulate a quality policy that closely reflects business objectives. Quality needs to be defined, interpreted, and clarified by writing a quality policy that includes a company’s mission, virtues, and statement of principles.
2. Quality Manual – The first piece of documentation a business will need to produce when introducing a QMS is a quality manual. It should clearly outline the specific reasons for QMS framework adoption and should simply define the function of quality within an organization.
3. Organizational Structure & Responsibilities – Structural models that define organizational configurations and responsibilities should be clear, concise, and easily interpreted. An organization characterized by a QMS incorporates both people and structure. The entire product lifestyle should be communicated in documentation that determines the path of workflow. Standard operating procedures (SOPs) are then linked to organizational charts which can be used to help define responsibilities.
4. Data Management – The success of a QMS framework is dependent on data quality and availability. Well-managed data helps to prevent dips in quality control and enables a culture of continuous improvement. Inadequate data management practices lead to inconsistencies in quality, operations inefficiencies, poor customer satisfaction, compliance risks, and low profitability.
5. Processes – Standardized processes are the basis for a good QMS system. Replicable procedures that are identifiable and easily defined are helping businesses to apply success metrics such as continual improvement and standardized output quality.
What Are The Different Types Of QMS?
There are various techniques for implementing quality control and assurance that can be easily integrated into a QMS:
Supply Chain Management (SCM)
Supply chain management enables businesses to effectively manage the cycle of goods and services from manufacturing all the way to the consumer. Customer satisfaction and the delivery of high-quality products rely on practical supply chain management that helps to reduce operational costs and increase profit margins.
Statistical Process Control (SPC)
Controlling and measuring quality in manufacturing is done through statistical process control (SPC). It’s an industry standard that collects data in real-time and maps out predetermined control limits. Control limits are gauged through the measured potential of the manufacturing process and can be used to determine functional operations.
Failure Mode & Effective Analysis (FMEA)
Design or manufacturing process deficiencies can be easily identified through failure mode and effective analytical tools.
Failure Modes are a collation of data that represents how a business or process might fail, especially when it impacts consumers.
Effective Analysis allows businesses to interpret the impact and outcome of failure, limit damage, and prevent decline.
Advanced Product Quality Planning (APQP)
Advanced product quality planning helps businesses to ensure quality and performance through the use of effective planning procedures. The APQP process is implemented by organizations that want to secure customer satisfaction concerning products and services. The standardized framework sets out quality requirements for suppliers and is primarily used to stimulate communication within the engineering process.
What Are The 7 Principles Of QMS?
1. Customer Focus – Quality management is defined as having a primary focus on meeting customer requirements and surpassing customer expectations. Customer retention is achieved with high consumer confidence and the guarantee of value for money. Interpreting and understanding existing and future customer needs is vital to the sustained growth and development of an organization.
2. Leadership – Creating a sense of unity that has motive, objectives, and goals provides businesses with the opportunity to steer their policies, strategies, and resources to achieve a greater purpose. Businesses that create sustainable working environments that offer engagement and enrichment benefit from better process coordination and increased efficiency.
3. Engagement of People – To deliver effectively, workers need to be engaged in providing inherent value. People who are motivated, competent, and empowered, create a form of intrinsic integrity that enhances the investment of personal development initiatives. Trust, collaboration, and employee satisfaction all play a major role in an organization’s quality objectives and culture.
4. Process Approach – Reliable results can be accomplished through the use of effective and efficient activities. These activities are interpreted and organized as companion processes that work by functioning as a coherent system. A QMS consists of interrelated processes that work to optimize business performance through the comprehension of processes, resources, interaction, and controls.
5. Improvement – Improvement is a key factor in maintaining growth and stability in the digital sphere. Organizations that factor improvement targets into their QMS can expect performance growth, the ability to react to external change, and the advancement of opportunity.
6. Evidence-Based Decision Making – Smart decisions that factor in evidence, analysis, and evaluation of data are crucial in improving the decision-making process. Performance and the ability to achieve objectives and operational efficiency are critical components of evidence-based decision-making that determine outcomes through the interpretation and analysis of data and information.
7. Relationship Management – Interested parties such as suppliers have a vested interest in the success of organizations they partner up with. They have a huge influence on sustained success, which is more feasible when strengthened relationships are used to optimize and impact performance.
What Is The Purpose Of A QMS?
The purpose of an effective quality management system is to guarantee the consistent application of methods, information, skills, and controls through the use of strategies, policies, and software applications to streamline processes and create uniformity.
The main focus of a QMS is to build and improve upon the quality of organizational output through the continued development, growth, and improvement of internal and external business practices.
What Are QMS Tools?
Quality management software tools are applications that facilitate and simplify business processes. They are used to integrate, automate and combine quality-based activities. Effective CMS tools enable organizations to build and align quality across product life cycles through the streamlining of important processes like risk management, documents control, and employee training.
What Are The 3 Stages Of Quality Management?
Quality Planning
Quality planning is used to determine the necessary quality standards and delivers valuable direction for businesses on how to interact and engage with stakeholders on quality management issues.
Quality Assurance
Quality assurance encompasses the entire product lifecycle and works to steer planning and control measures to meet protocols and guidelines through measurable performance initiatives. Frequent audits and regular reviews are carried out to provide assurances to stakeholders.
Quality Control
Quality control provides a measurement of how well businesses are delivering on projects and meeting specifications. Deliverables need to adhere to strict laws on corporate governance and limit project disunity through a systematic strategy that understands the problem and maintains the implementation of a fixed approach.
What Is The Connection Between QMS & Digital Transformation?
Quality management systems play an important role in digital transformation and help to optimize long-term business performance. Enhanced visibility helps to ensure quality, collaboration, and decision-making. The digital revolution has transformed the way we use and leverage digital technologies. It’s being utilized by businesses from around the world to enhance business models, streamline processes and reinforce activities.
When workflows are automated, it results in heightened profitability, productivity, and employee retention. Industry 4.0 has ensured wider availability and access to digital processes via smart network devices that have much quicker access to data.
A QMS is an imperative part of any modern digital transformation strategy. It allows businesses to streamline processes and keep track of quality and value. Quality management systems are an essential tool for modern businesses that want to identify quality issues, remove needless actions, and bridge performance gaps.