Quality is essential for any successful organization. It sets the standards expected by customers and stakeholders. Total quality management (TQM) is a structured way to improve an organization’s processes. Its goal is to enhance the quality of goods and services through business process reengineering.
When done right, TQM helps companies produce products at a lower cost. It also leads to more consistent products, which builds stronger customer loyalty. By focusing on quality and reducing waste, businesses can achieve better results.
In this article, we will explore 13 key benefits of implementing TQM in your organization.
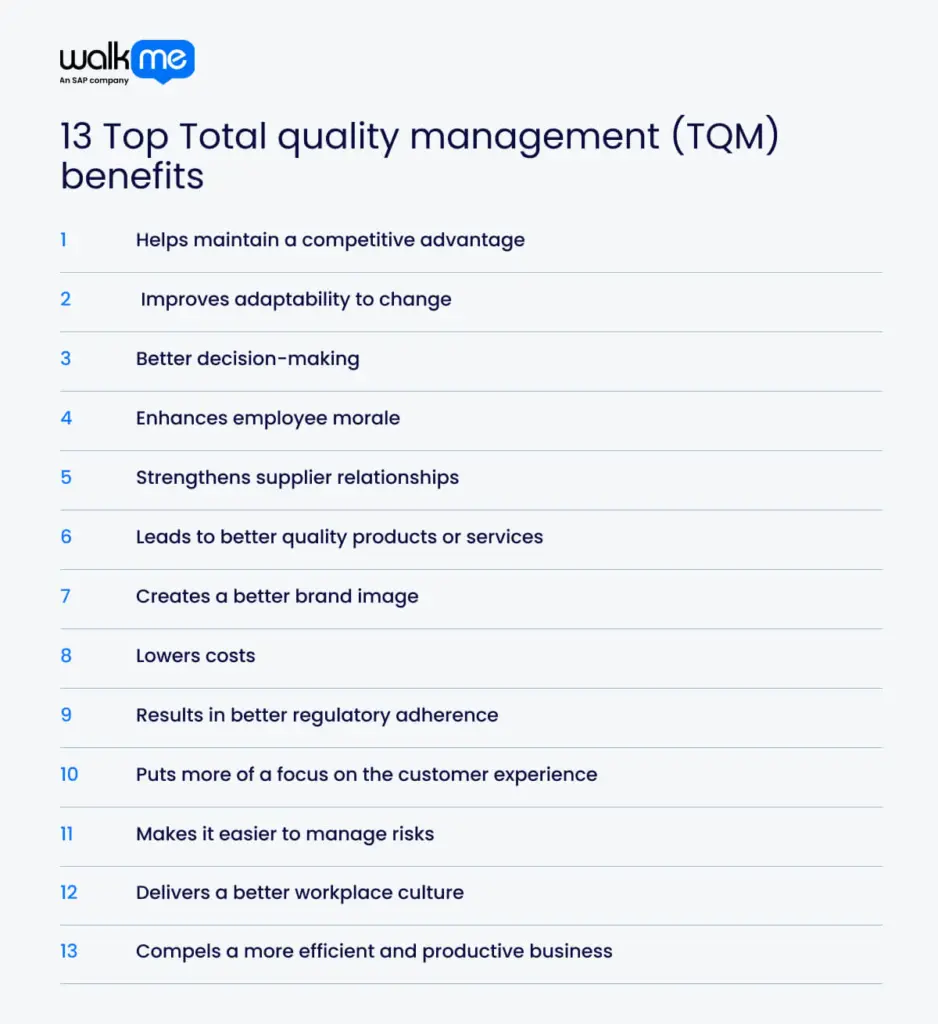
1. Helps maintain a competitive advantage
High-quality products and services can give your business a big advantage. Customers are attracted to reliable businesses that offer excellent products, which can lead to higher profits and a bigger market share.
Total Quality Management (TQM) helps you find and fix problems to improve your processes. Over time, this makes your business more efficient and improves the quality of your products and services.
TQM helps lower production costs by reducing waste and mistakes, which means higher profits for your business.
2. Improves adaptability to change
TQM helps organizations stay flexible by always looking for ways to improve. By constantly learning, businesses can adapt to changes in technology, the market, and customer needs.
Involving employees in solving quality problems creates an active and engaged workforce. This helps companies adapt quickly to new situations.
Using data to find areas for improvement is a key part of TQM. Data-driven decisions make it easier to respond and adapt when needed.
TQM’s focus on improvement encourages regular evaluations and refinements. This makes processes more efficient and better suited to changing demands.
3. Better decision-making
TQM is about using data to make decisions. This helps to reduce risks and leads to better outcomes. By collecting and analyzing data, companies can identify trends and fix problems early. This helps to improve quality and make better decisions.
Its focus on continuous improvement means regularly analyzing data to make sure decisions are based on the latest information.
Understanding customer needs is a key part of this strategy. Decisions about products and services are made with these needs in mind.
TQM also provides tools to find the root causes of problems. These tools help to create targeted solutions and improve decision-making.
4. Enhances employee morale
Poor communication can hurt a company’s performance and growth. It can lead to misunderstandings, lower productivity, and wasted time, and it can also make employees feel less motivated.
TQM helps to improve communication between different departments and levels of management. It helps to build stronger teams and boost employee morale. By encouraging employees to share their ideas, TQM helps them feel more invested in their work. This leads to greater job satisfaction.
TQM also promotes teamwork by creating groups that work together to improve quality. These teams create a more supportive environment and help people to connect with each other.
Additionally, continuous improvement helps employees learn new skills. This gives them a sense of accomplishment and personal growth. Regular feedback and recognition further boost morale and motivation.
5. Strengthens supplier relationships
TQM encourages working closely with suppliers to make sure they provide high-quality materials and parts. Strong relationships based on trust and shared goals help to make the supply chain more reliable.
By working together to set quality standards and focus on continuous improvement, businesses can reduce mistakes, delays, and costs.
Using data to track supplier performance helps to identify areas for improvement. This allows businesses to make better decisions about which suppliers to use and how to manage them.
When quality problems occur, TQM encourages working with suppliers to find the root cause and fix the problem. Regular communication helps spot potential problems early, improve coordination, and provide timely feedback.
6. Leads to better quality products or services
One of the biggest benefits of TQM is that it helps improve products and services. By focusing on making customers happy and improving processes, businesses can reduce mistakes. This means that products meet or even exceed expectations, which improves customer engagement.
Everyone in the company, from top to bottom, is encouraged to contribute to improving quality. They share their ideas and knowledge to help solve problems.
Keeping an eye on how things are made is a big part of TQM. This helps to find potential problems early and fix them before they become bigger issues.
Data is used to make decisions in TQM. By analyzing data, businesses can see trends, find areas for improvement, and track the effectiveness of their quality efforts.
7. Creates a better brand image
Customers who experience a company that uses TQM will notice a better brand image and reputation. This can lead to more sales as happy customers tell their friends and family.
Improving products and processes shows that the company cares about quality and can adapt to change. Customers see this as a positive quality in a brand.
When employees are involved in improving quality, they help ensure excellent service. This makes customers happy and strengthens the brand.
By reducing mistakes during production, customers receive better-quality products. This helps to minimize complaints and negative feedback.
TQM also promotes transparency by having clear quality standards. This builds trust with customers and boosts the brand’s image.
8. Lowers costs
TQM helps businesses save money by finding and fixing quality problems early in the process. This reduces the need to redo work, throw things away, and deal with returns, which saves on materials and labor costs.
It also reduces unnecessary steps, reduces waste, and manages inventory better. This leads to less waste of materials and time.
By analyzing how work flows, TQM can find bottlenecks and inefficiencies. This makes operations smoother and more productive.
Involving employees in quality improvement is a big part of TQM. When employees are involved, they take more responsibility and make fewer mistakes.
Rather than fixing problems after they happen, TQM focuses on preventing them. This proactive approach is more cost-effective.
9. Results in better regulatory adherence
Many businesses need to follow rules and regulations. TQM can help companies meet these standards. For example, in manufacturing, TQM helps make sure products are safe and work properly before they’re sold.
TQM creates a culture where everyone helps to keep things safe and legal. Everyone knows their part in following the rules and reporting problems.
It also encourages continuous improvement, which helps businesses make their processes better and meet regulations.
Keeping good records is important in TQM. This helps ensure that information is accurate and easy to find during inspections. TQM also helps to find and fix problems early, which can prevent bigger issues later.
10. Puts more of a focus on the customer experience
TQM is all about putting customers first. By focusing on their needs and always striving to meet them, companies can build stronger relationships.
Happy customers tend to stick around, which helps businesses grow. TQM also helps everyone in the company understand what customers want and work together to make them happier.
To improve, companies use customer feedback to find areas for improvement, such as their products, services, and work. TQM encourages a mindset of always improving, making small changes based on what customers say and what the data shows.
It also encourages different teams to work together to meet customer needs.
11. Makes it easier to manage risks
TQM helps businesses find and fix problems early, reducing the chance of mistakes and big problems. By examining how things are done and how well they’re done, businesses can identify risky areas and make plans to deal with them.
It also encourages employees to report risks and suggest improvements. This helps to better understand potential problems and work together to solve them.
Businesses using TQM look at the root causes of mistakes. Fixing these problems not only solves current issues but also helps prevent similar problems in the future.
12. Delivers a better workplace culture
TQM is based on teamwork, good communication, and always learning. These things help to create a positive and friendly work environment. A strong organizational culture helps the company reach its goals.
Everyone in the company needs to be committed to TQM. This means businesses often spend time figuring out what their core values are. These values guide how things are done every day and improve communication. Over time, they become part of the company’s identity.
Recognizing and rewarding employees is another important part of TQM. Celebrating people’s contributions motivates them and encourages good behavior.
When employees understand how they help to deliver quality, they feel more engaged and connected to the company’s goals.
13. Compels a more efficient and productive business
Total Quality Management (TQM) is a way to make things more efficient by focusing on what customers want. It helps to cut out unnecessary steps, reduce mistakes, and waste less. This ensures that products meet the needs of the market.
TQM examines how things are done to find ways to make them smoother and faster. Employees are encouraged to contribute to improving quality, which can boost their motivation and problem-solving skills. Motivated employees often work harder, leading to a more productive and efficient workplace.
Data is used to make decisions in TQM, helping to identify and measure improvements. The goal is to always improve, find better ways to work, and avoid getting stuck.
In addition, TQM helps to reduce mistakes, lower costs, and deliver high-quality products. Happy customers and engaged employees lead to better productivity and long-term success.
Enhance your efficiency and profitability with total quality management (TQM)
TQM (Total Quality Management) is a way to improve everything in a company. By focusing on quality, companies can make their customers happier. When things run smoothly, and without mistakes, customers are more satisfied.
It aims to reduce errors, make processes more efficient, and improve overall performance. Companies that stick with TQM over time often see big improvements.
One of the best things about TQM is that it creates a culture of continuous improvement. This helps companies adapt to change and stay ahead of the competition.
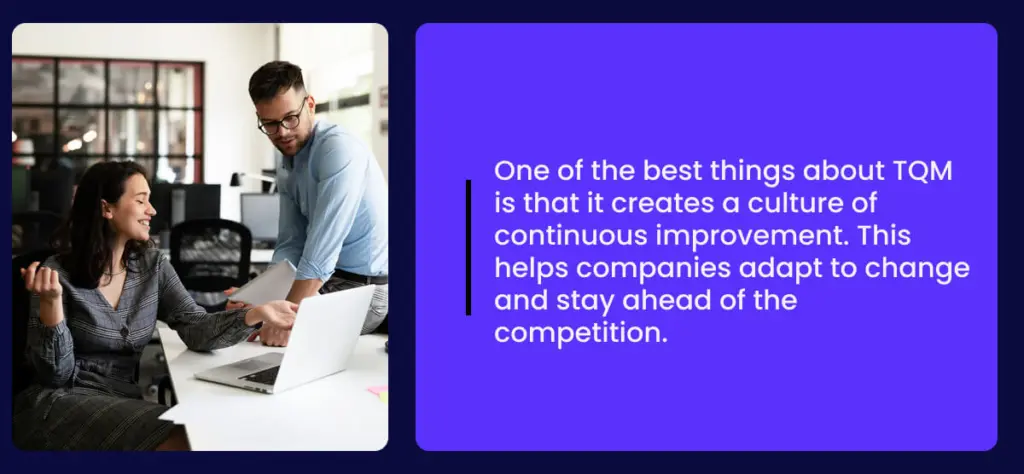
TQM is not a one-time fix. It requires ongoing effort. By following TQM principles, involving employees, and constantly making improvements, companies can ensure their success in a changing market.