Forget smokestacks and assembly lines – the factory of the future is wired, data-driven, and humming with digital intelligence. Industry 4.0, propelled by automation, artificial intelligence, and the Internet of Things, is no longer a futuristic buzzword but a transformative reality for successful manufacturing enterprises.
From Siemens’ self-aware robots to Rolls-Royce’s engine whisperers, digital transformation in manufacturing pioneers isn’t just tweaking processes – they’re rewriting the production-line playbook, paving the way for a smarter, more agile, and customer-centric future.
Prepare to witness the evolution of making things, where efficiency and innovation collide to reshape the industrial landscape through strategic digital transformation in manufacturing.
This article will explore digital transformation in manufacturing, covering its definition, the significance of digitalization in manufacturing, the transformative impact of Industry 4.0 technologies, best practices for digital transformation in manufacturing, and some notable examples of successful implementations.
What is digital transformation in manufacturing?
Digital transformation in manufacturing involves an enterprise implementing new digital technologies to optimize and improve manufacturing processes. The process can be an organizational approach or involve focusing on technologies that need improvement to optimize organizational success using digitization to outcompete other organizations.
Enterprises often use IoT (Internet of Things), additive manufacturing, and artificial intelligence (AI) to streamline processes, enabling them to design and manufacture products more quickly than ever, increasing revenue and customer experience.
Why is digitalization important in manufacturing?
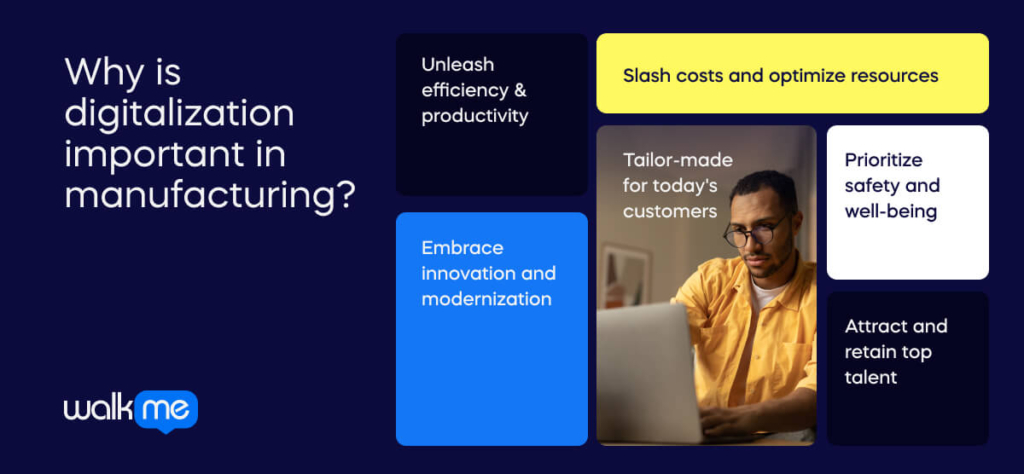
There are six main reasons digitalization is essential in manufacturing in the list below, beginning with unleashing efficiency and productivity. Consider these points when discussing whether digitalization is necessary for your organization.
1. Unleash efficiency & productivity
Eliminate paper-based processes and leverage the scalability and agility of cloud-based solutions to enhance your operational efficiency to see the following benefits significantly:
- Streamlined processes: Automating repetitive tasks frees up your team for creative work.
- Smarter decisions: Data-driven insights lead to better choices, minimizing costly errors.
- Effortless performance tracking: Monitor progress in real-time, identifying bottlenecks and opportunities.
- Pre-test, refine, win: Test new ideas before scaling, eliminating wasted effort and maximizing profits.
Explore digital tools to achieve the above, like:
- Online forms and approvals.
- Automatic inventory management.
- Virtual factory simulations.
- Digital supplier sourcing.
- Collaborative planning platforms.
- Real-time communication software.
2. Slash costs and optimize resources
Digital manufacturing sheds light on inventory, deliveries, and demand patterns. You’ll navigate market fluctuations with ease, reducing:
- Excessive inventory: Stock what you need when you need it.
- Material waste: Precision planning minimizes leftovers and scrap.
- Operational downtime: Predictive maintenance keeps machines humming.
3. Embrace innovation and modernization
Investing in digital infrastructure isn’t just about cost savings; it’s about empowering your people. Imagine:
- Tech-savvy workforce: Equip your team with cutting-edge tools to boost their effectiveness.
- Enhanced collaboration: Connect everyone, share ideas, and spark innovation across departments.
- Accelerated development: Streamline processes and bring new products to market faster.
4. Tailor-made for today’s customers
Digital manufacturing unlocks exciting customization options for your customers. Offer unique products while maintaining mass production efficiency for a competitive edge.
5. Prioritize safety and well-being
Let robots handle hazardous tasks, protecting your human workforce. Intelligent sensors detect and warn about potential risks, keeping everyone safe.
6. Attract and retain top talent
A digital work environment attracts and inspires skilled professionals in today’s tech-driven world. Join the future of manufacturing and build a team that thrives in innovation.
How are industry 4.0 technologies transforming manufacturing?
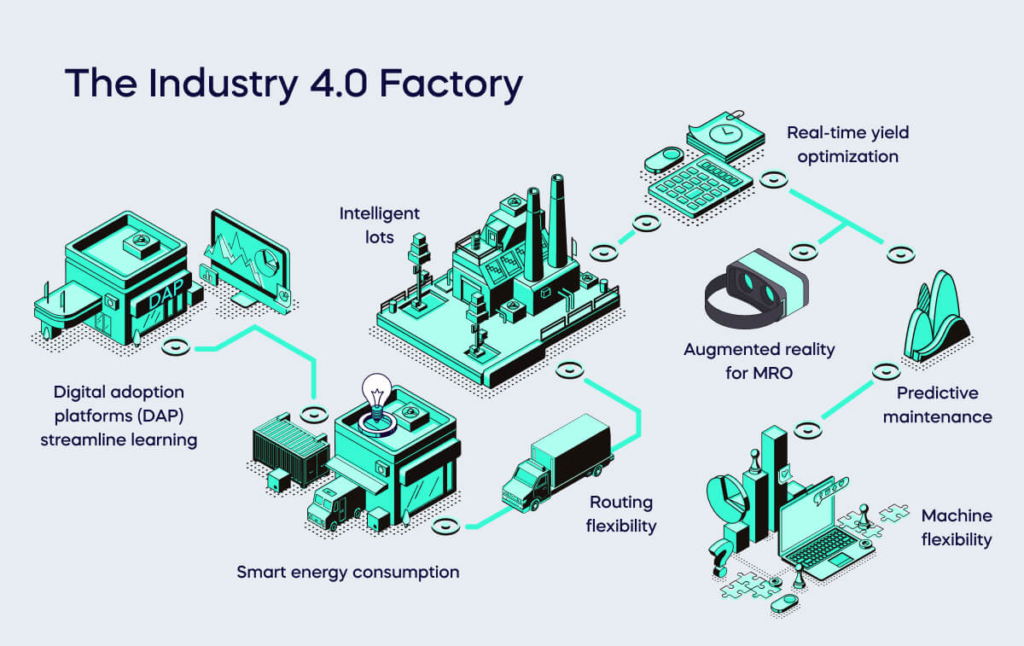
The industrial landscape is profoundly transforming, driven by the adoption of Industry 4.0 technologies. This digital revolution promises significant efficiency, productivity, and adaptability gains, paving the way for your manufacturing enterprise’s brighter and more resilient future.
Digital adoption platforms (DAP) streamline learning
A digital adoption platform (DAP) is like the Rosetta Stone of Industry 4.0, seamlessly translating advanced tech like digital twins and AI into actionable insights for your team as they adapt to the challenges of a digital workplace.
A DAP eliminates clunky manuals and siloed data as they guide users through each step, building confidence and unlocking the true potential of automation using in-app guidance to allow employees to learn as they work.
The result is optimized production, reduced errors, and agility to adapt to ever-changing demands while improving employee experience. For these reasons, a DAP isn’t just an optional extra in the face of the Industry 4.0 revolution. It’s the key to unlocking your manufacturing superpower.
Smart energy consumption
Imagine a factory where energy usage is no longer a mystery. Automated building management systems equipped with sensors and intelligence provide real-time insights into energy consumption across machinery, lighting, HVAC, and fire safety systems.
This holistic view, combined with external data like weather forecasts and electricity prices, empowers informed decision-making.
Seattle Union Station sets a green standard with its LEED Platinum certification, achieved through innovative eco-friendly practices. Notably, the station deploys non-VOC cleaning solutions, fosters sustainable transportation with electric vehicle charging and bike racks, and optimizes energy consumption with a centralized airflow system.
Intelligent lots
Industry 4.0 fosters innovative supply chains through “intelligent lots.” Innovative information embedded in products and pallets empowers just-in-time manufacturing. RFID tags, sensors, and various connectivity technologies like 3G, LoRa WAN, and Wi-Fi track items like containers and pallets throughout their journey.
Real-time yield optimization
Imagine a network of sensors, software, and connected equipment providing an instantaneous snapshot of machine performance.
By harnessing the power of machine learning, transformation officers can work with the IT teams and business intelligence team members to turn this data into real-time yield optimization. Continuously recalibrating outputs based on various factors ensures peak efficiency.
Routing flexibility
Modern manufacturing demands adaptability. Flexible manufacturing systems powered by IoT enable companies to respond dynamically to changing customer needs. Routing flexibility allows manufacturers to cope with disruptions like equipment breakdowns by shifting production routes or utilizing multiple machines.
Hierarchical job shop models and dynamic simulations empower this adaptable approach, maximizing asset utilization and uptime.
Machine flexibility
As Industry 4.0 decentralizes and autonomizes manufacturing, machine flexibility becomes key. Standard interfaces and intelligent infrastructure pave the way for a modular approach to automation.
“Plug and produce” modules enable swift reconfiguration of production lines. Imagine robotic arms with quick-fit data/communication cables or high-level sensors, eliminating the need for traditional modules. Such flexibility translates to dynamic and intuitive maintenance.
Remote monitoring and control
Manufacturing plants are intricate ecosystems. When operations span global networks, real-time visibility becomes crucial. IoT architecture equipped with dashboards and mobile access empowers engineers to monitor individual assets remotely from anywhere in the world.
Predictive maintenance
Data-driven insights fueled by sensors and machine learning revolutionize maintenance. Instead of calendar-based or reactive approaches, manufacturers can now spot potential problems before they occur.
Augmented reality for MRO
Maintenance manuals are giving way to augmented reality headsets. Imagine technicians equipped with these devices receiving real-time data, diagrams, and instructions overlaid on their field of view.
These are just a few examples of how Industry 4.0 is transforming manufacturing. By embracing these smart technologies, manufacturers can unlock a new era of efficiency, productivity, and adaptability, laying the foundation for a future where innovation and resilience reign supreme.
Digital transformation in manufacturing best practices
Follow these top five best practices to ensure successful manufacturing digital transformation. The first of these best practices involves making decisions augmented by digital twins in the design process for new products.
Make confident decisions with Digital Twins
Imagine a living copy of your product or process, constantly learning and evolving alongside its physical counterpart, and you will understand the power of a digital twin.
It offers real-time insights, faster decisions, and optimized production, leading to superior products and customer satisfaction. Industries across the board are reaping the benefits, with the digital twins market likely to grow to USD 137.6 billion by 2030.
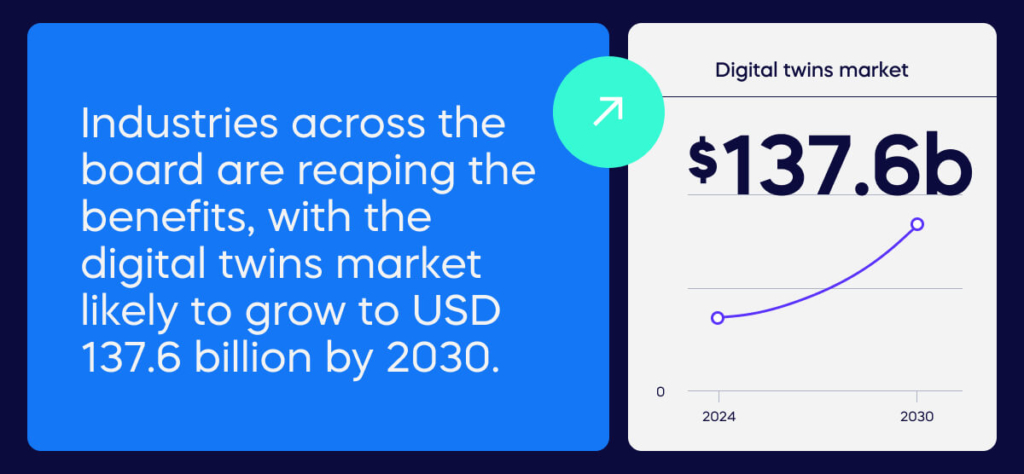
Break down silos with vertical integration
Think of your factory as a well-oiled machine where data flows seamlessly from the shop floor to the top floor. Vertical integration bridges the IT and operational technology gap, bringing real-time production data to strategic decision-makers.
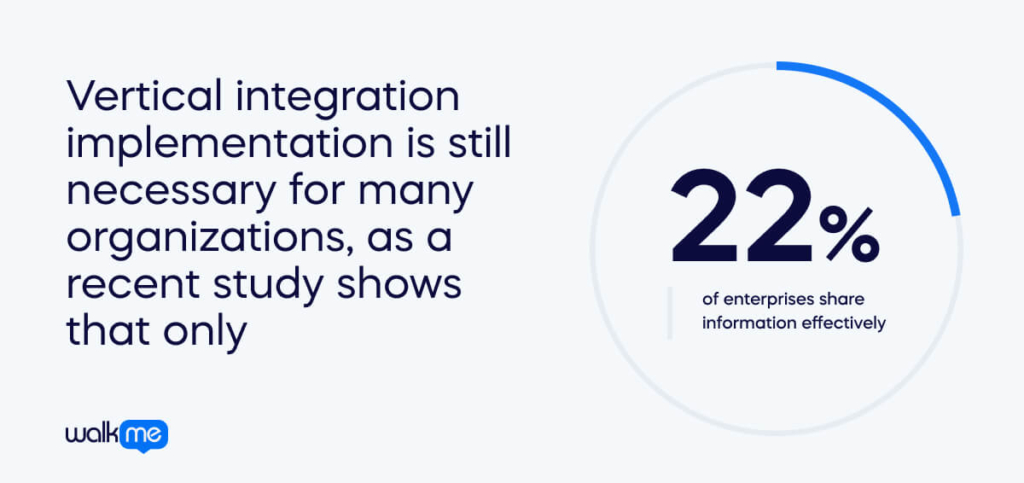
Connect the dots with horizontal integration
Forget information silos. Horizontal integration weaves a digital thread through your entire value chain, from design and production to service and recycling. It can help you expand your market reach, reduce competition, and achieve economies of scale.
This holistic approach eliminates data barriers, fostering collaboration and innovation across the entire spectrum.
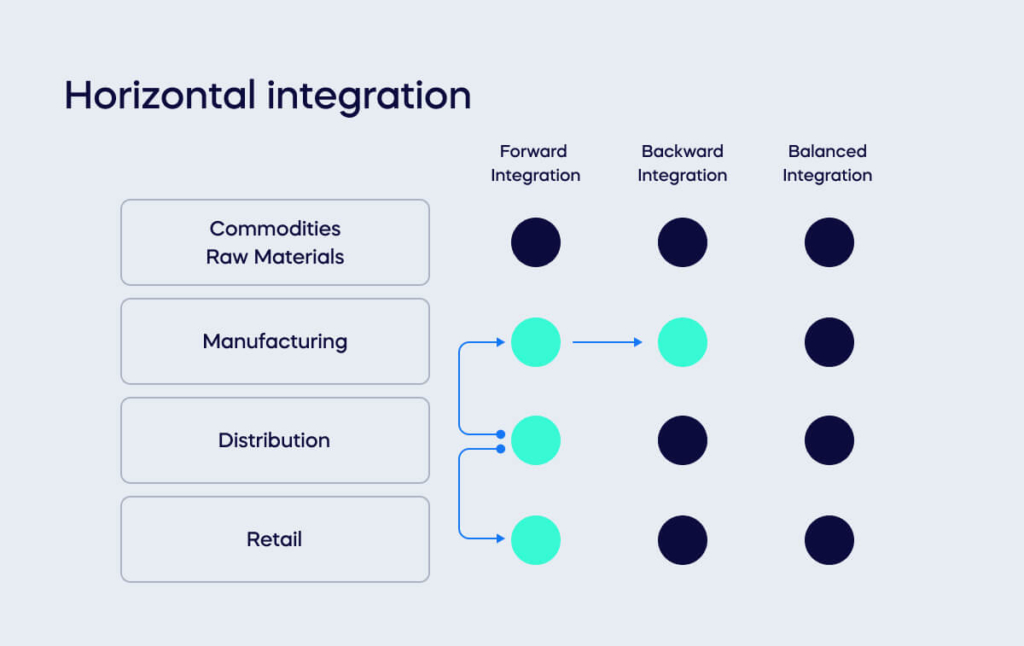
When a company acquires or invests in suppliers, it’s backward integration (moving upstream). Taking control of distribution or retail is forward integration (downstream). Balanced integration involves mergers or investments in both directions.
Unleash growth with automation
Imagine streamlined operations, fewer errors, and increased efficiency. Automation unlocks this potential, propelling your business to new heights. Some benefits are reduced costs, boosted employee morale, and improved customer experience. A staggering 97% of IT managers consider automation essential for digital transformation.
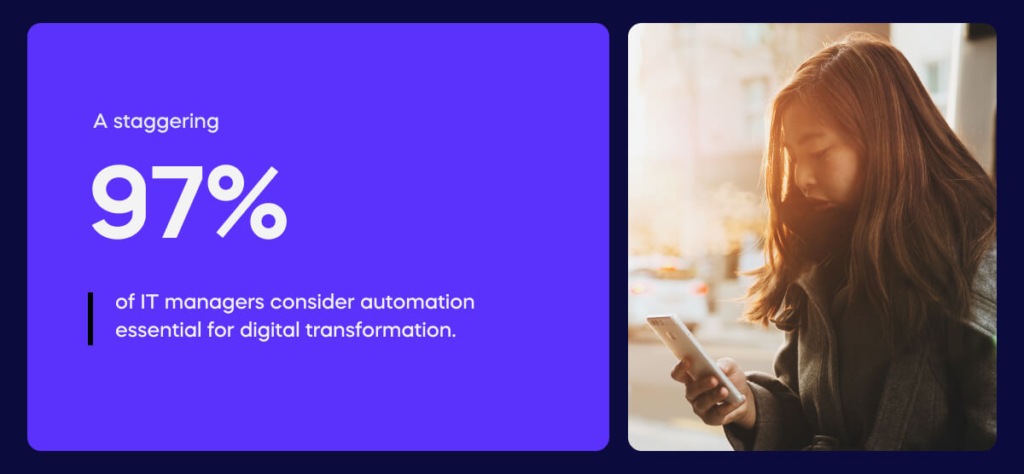
Embrace innovation with additive manufacturing
Revolutionize your approach to production with additive manufacturing (AM). This groundbreaking technology shapes complex geometries with minimal waste, saving time, materials, and energy.
It fosters sustainable practices, promotes mass customization, and shortens product development cycles. Studies estimate that a large share of this market will be in the 3D printing metal market, with companies likely to spend USD 5.5 billion by 2026.
Examples of successful digital transformation in manufacturing
In the age of Industry 4.0, manufacturing giants are shedding their steel skins and embracing a radical digital metamorphosis. Consider the three success stories below, uncovering how automation, data, and smart strategies are forging a new era of efficiency, resilience, and customer-centricity.
Siemens Amberg factory: A vision of the future
With extensive automation and real-time tracking through RFID technology, every product moves through production with remarkable precision. This step minimizes errors and allows for agile adjustments to fluctuating customer demands, ensuring a responsive and efficient operation.
Rolls-Royce: Avoiding downtime, maximizing uptime
This proactive approach, exemplified by Rolls-Royce’s engine health management system, minimizes downtime, reduces maintenance costs, and ensures the highest levels of operational safety.
Amazon: Supply chain agility
Advanced automation, such as Amazon’s robotics workforce, increases efficiency and speed throughout the logistics process. Using this tool translates to quicker customer deliveries, lower company operational costs, and a more resilient and responsive supply chain ecosystem.
Embracing these digital transformation trends, manufacturers can gain a competitive edge, optimize operations, and navigate the ever-evolving demands of the modern marketplace.
Kickstart your manufacturing digital transformation with a DAP
When planning your digital transformation for your manufacturing enterprise, don’t forget that staff, not technology, drives any successful large-scale changes. A digital adoption platform (DAP) is your rocket to Industry 4.0 success.
DAPs bridge the gap between technology and your team, guiding users through new systems like digital twins and AI, boosting adoption, and unlocking efficiency gains you never dreamed of.
Forget clunky manuals and frustrated faces – they make digital transformation a party, propelling your manufacturing into the future, one empowered employee at a time. So, ditch the papercuts and grab the pixels – your competitive edge awaits, courtesy of a DAP.
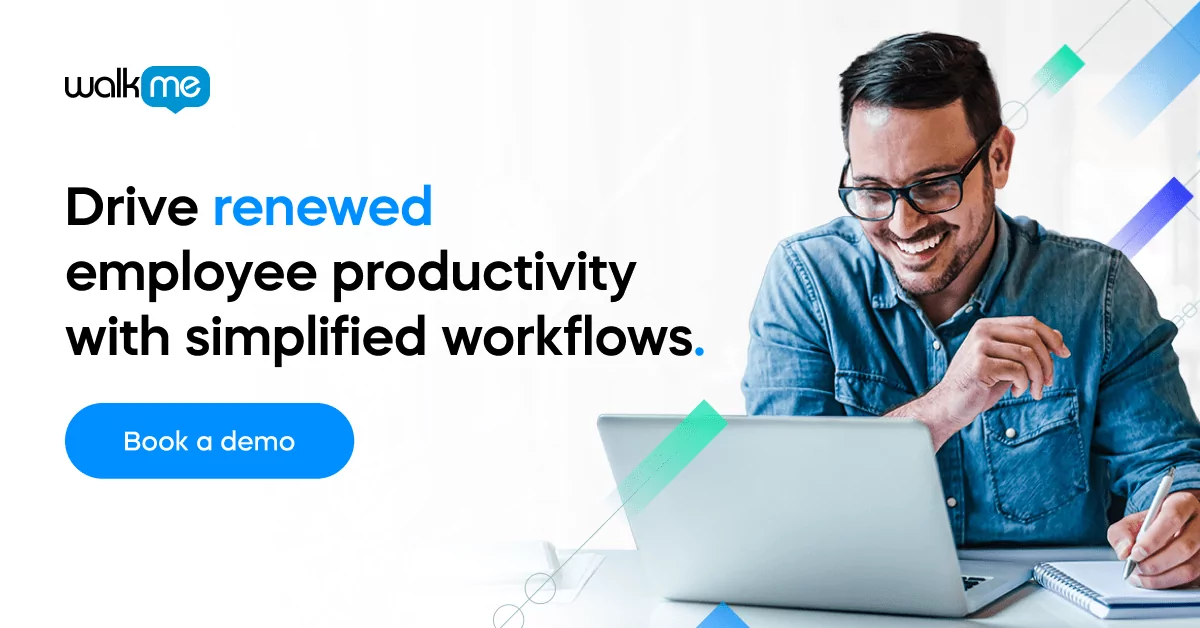